Bernie Peet is president of Pork Chain Consulting Ltd. of Lacombe, Alberta, and editor of Western Hog Journal. His columns will run every second week in the Manitoba Co-operator.
Diseases such as PRRS, swine influenza and mycoplasma cost the North American pork industry hundreds of millions each year. For producers of swine genetics, including boar stud operators, the threat of infection with these diseases is ever present.
Over the last few years, air filtration has been tried as a means of reducing aerosol transmission of these diseases, with a high degree of success, according to Dr. Darwin Reicks from the Swine Vet Center, St. Peter, Minnesota. Speaking at the Banff Pork Seminar in January, he said that true HEPA filters are 99.9 per cent efficient at removing particles down to 0.3 microns. Although the organisms that cause disease are smaller than 0.3 microns, they are carried on particles larger than this which are removed by the filter.
Read Also
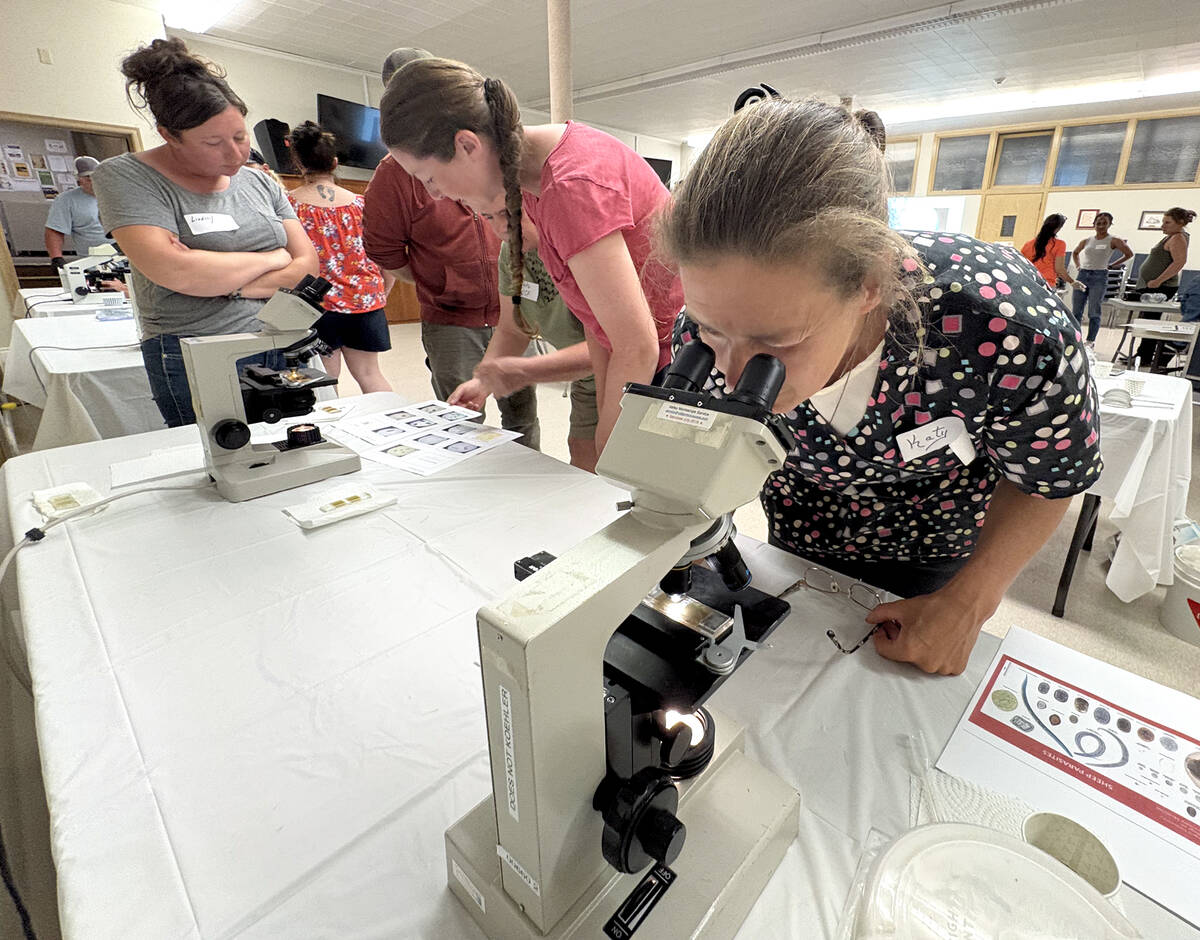
Smart deworming for sheep starts with individual fecal egg counts
Fecal egg count tests are one step to managing dewormer resistance and managing sheep parasites on Canadian sheep farms to maintain flock health.
PRACTICAL CHALLENGES
There are some practical challenges to air filtration, especially where it is required year round. In hot weather the ventilation requirement is much higher, so the area of filter required to push the air through also increases. Many barns in the U. S. Midwest switch to using “tunnel” ventilation in summer. With this system, all air comes in through an opening at one end of the building and exits at the other end.
“This involves the construction of a filter bank in front of the cool cell, which adds construction cost,” Reicks says. “In addition, these facilities normally pull air through ceiling inlets in the winter so filters also need to be mounted on top of each inlet box.”
As a result, the cost of a filtration system for these facilities, including construction for the filter banks, has been $180-$200 per animal.
Air conditioning systems, which are becoming more common in boar studs, greatly reduce the number of filters needed.
“This is because the air comes in cool year round, therefore the summer ventilation needs are more similar to wintertime,” Reicks says.
Some producers have opted for partial filtration, which is cheaper but increases the risk of aerosol infection. “Many sites simply put a filter above each of the ceiling inlets,” Reicks says. “With this system, the air flow is adequate until the outside temperatures generally reach 65-70 F. After that point, there is too much restriction and they must either remove the filters or utilize air coming through a cool cell.”
With partial filtration, air is not filtered in hot weather conditions, which increases the risks, but during such conditions, the risk of aerosol introduction of PRRS is reduced anyway, Reicks says.
GOOD RETURN ON INVESTMENT
Reicks says 33 farms within his practice have installed filtration systems, 18 of which have 100 per cent filtration and the rest partial filtration. There have been three PRRS breaks on farms using partial filtration, all when the air was not being filtered. There was one PRRS break on a farm with 100 per cent filtration, which is believed to be the result of a transportation biosecurity breach or heavily damaged filters.
There were two swine influenza breaks on 100 per cent filtered farms, but no mycoplasma breaks.
“An important consideration for us from the start has been that we shouldn’t expect to never have a PRRS break just because we installed air filtration,” Reicks explains. “However, if we can reduce the incidence of PRRS breaks significantly, it would be good return on the investment. This has proven to be the case, in our experience.”
Reicks says that for boar studs, filtration has now become the standard, except for studs with no history of PRRS and located five miles or more from other pigs.
NEW FILTER FROM QUEBEC
A new Canadian-made air filter has recently been evaluated by Dr. Laura Batista from the Faculté de médecine vétérinaire de l’Université de Montréal (FMV) and the team of the Centre de développement du porc du Québec inc. (CDPQ; Quebec Swine Development Centre). It is not only efficient at stopping the entry of PRRS virus, but is more cost effective than existing systems, she says.
Canadian company Noveko Inc. recently developed an innovative filter combination which integrates a viricide, bactericide and fungicide at the molecular level into the fibre of the filter material.
“Compared to other filters on the market, this filter is very flexible in its use and installation because it comes in rolls of a very flexible, washable and easy to maintain material,” Batista says. “Not only does it block the passage of bioaerosols due to its filtering effect, but it also has the ability to neutralize pathogens as they come in contact with the antimicrobial agents embedded in the filter fibre.
The filtration system is contained in a frame having three levels of filtration: Level 1, an insect screen, removes large particles and is easy to clean. Level 2 has three layers of the patented filter material containing the viricide, bactericide and fungicide cocktail. This level removes fine dust particles and initiates the filtration and neutralization process which reduces the number of times Level 3 needs to be cleaned. Finally, Level 3 contains seven layers of the filtering and neutralizing material. The cost per inventoried sow per year over a period of 10 years is around C$26-$27.
While the new system overcomes some of the problems of previous equipment, air filtration is not the “magic bullet,” Batista warns. “It is one more gadget in our biosecurity tool box, but before thinking of investing in air filtration you definitely have to have basic biosecurity measures in place.”