It looks like any other shipping container, but what’s inside could help boost food security in remote areas of the country one day.
Biosystems engineers at the University of Manitoba are perfecting a self-contained unit which includes a biomass boiler that produces up to 56 kW of heat. The unit also has a Stirling engine integrated into the system that utilizes the heat to generate up to five kW electricity.
That electricity will be used to power an LED lighting system in the Alternative Village greenhouse, to research the use of an alternate energy source for greenhouses in northern communities or off-grid locations.
The unit is a first of its kind in Canada supported with funding from the Canadian Foundation for Innovation.
New fuels
One of the long-term research objectives is to investigate the use of alternative biomass fuels such as straw, hemp and other plant material for use as pellets for the biomass fuel for the combined heat and power unit.
“There are other biomass boilers out there but this is the only one that we’re aware of in Canada that’s combining electrical power generation with heat,” said Kris Dick, associate professor in the university’s biosystems engineering department and founder and director of the campus Alternative Village.
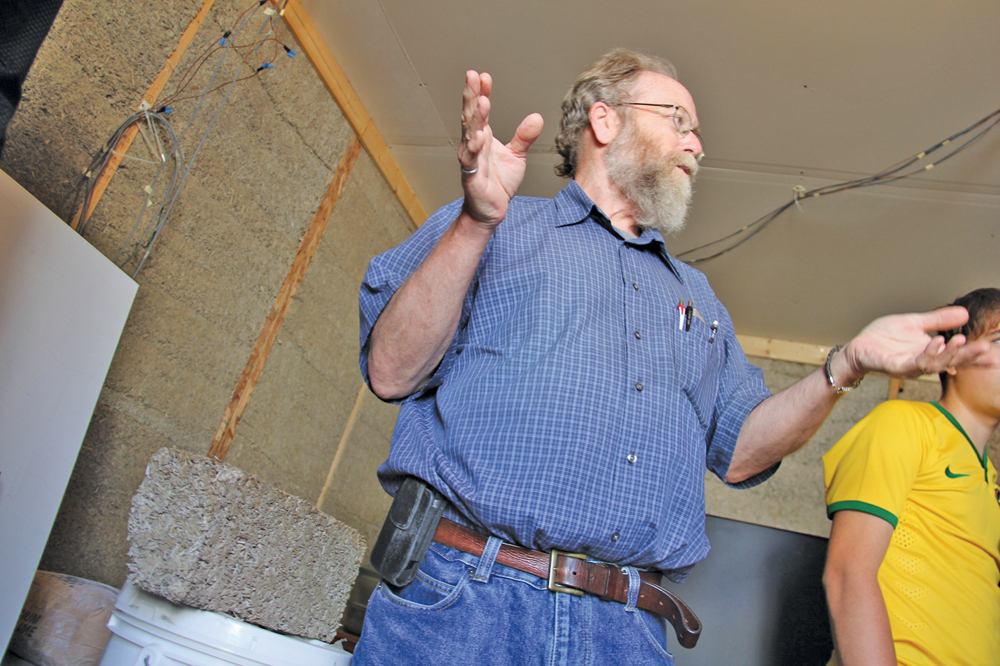
The site was visited earlier this month by other engineers in Manitoba, as part of a week-long conference of the Canadian Society for Bioengineering (CSBE) meeting in Winnipeg to discuss new approaches to the world’s food, fuel and fibre needs.
The Alternative Village is where university students get hands-on design and building experience, testing new concepts while working with non-conventional building materials such as straw, flax, compressed earth, hemp and biocomposite materials made from them.
Central to the Alternative Village is its 4,200-sq.-ft. Biosystems Strawbale Research Facility built in 2004 as a site to do research in and on. The research site has evolved around it and today is where new companies bring building concepts to evaluate.
Read Also
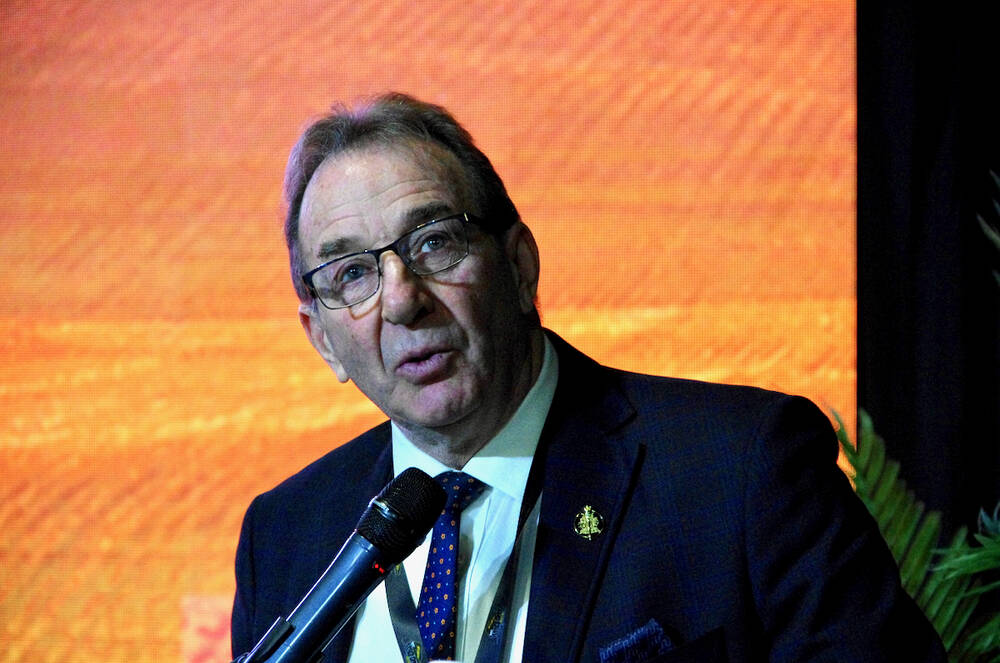
AgriStability enrolment deadline extended
The deadline for Manitoba farmers to enroll in the AgriStability business risk management program has been extended by three months agriculture minister Ron Kostyshyn announced on Friday.
“We provide a way to come in and do a little exploratory research to see if an idea is worth taking to the next stage,” said Dick. “My initial intent was that this would be a facility for small business and small industry, that do not have deep pockets, to come and investigate their ideas.”
Student focus
A very important part of the village is that students are actively engaged in all facets of the research from concept, construction of test equipment to the testing, he added.
“In my opinion, it is critical to combine theory with hands-on experience in the engineering education.”
The site, which is located on 1-1/2 acres of the campus, today includes multiple small structures where that research helps answer questions those writing building codes, insurers and financial institutions have when builders want to use alternative building materials.
Industry-sponsored research grants support the work at the Alternative Village (AV), allowing them to support graduate and undergraduate students along with equipment and materials, explains Dick.
Built in Manitoba, there is a greenhouse modelled after designs used in China, that features a back wall of 18 inches of straw and six inches of rammed earth, designed to absorb solar energy and release it back into the space, reducing the need for supplemental energy.
It’s a warm place even on a chilly Manitoba winter day. In -20 C in February with the sun, temperatures can rise to 45 C in the rammed earth back wall. They’ll be linking up the heat and power unit to work with this site.
“The heat in the greenhouse depends on the amount of solar radiation and time of year,” Dick said. “With a combined heat and power unit we can get a feel for how much (more heat) we will need in here to supplement it.”
Other structures include its ‘hempcrete’ building, made with panels constructed from a blend of chemicals, hemp hurd and stone. There are also buildings made from structural insulated panels, dense-packed cellulose in wood frame and cast-in-place PVC and foam wall systems.
That site is used to evaluate moisture movement through the building’s wall system as well as studies on heat transfer through various wall systems, Dick said.
“I’ve done studies that have compared the thermal resistance (R value) of structural insulated panels, dense-pack cellulose and concrete with exterior foam, compared to typical wood frame construction with fibreglass batt insulation.”
Biomass uses
The Alternative Village is also home to the ‘Green Garage,’ a 16×24 single-car garage, funded through Manitoba Agriculture, Growing Forward, and the Winnipeg-based Composites Innovation Centre.
Research, co-ordinated by Alternative Village’s biosystems students and the site’s technician, is focused on Manitoba-grown biomass. It aims to demonstrate the use of ag-fibre products such as soy-based biocomposite roof panels and hempcrete.
Other materials being studied include recycled fibreglass, experimental biocomposite window panes, siding made completely of recycled wood, and an alternative cement floor that actually has no cement in it. It’s made strictly from chemical and stone and is very sensitive to temperature.
“It pours out looking just like soup and will set up in 20 minutes,” said Dick.
The goal of the Green Garage is learning how all these materials perform and interact together while having a site to continuously build on understanding how to use alternative methods and materials.
The August conference — entitled Food, Fuel and Fibre for a Sustainable Future attracted biosystems engineers from around the world and featured four days of workshops and speakers, plus tours.
In Manitoba there are about a dozen biomass suppliers and pelletizers and approximately 40 biomass heating installations in greenhouses and Hutterite colonies.
Learning curve
Speakers asked during the conference to comment on why the biomass industry isn’t further ahead, say market demand remains a big part of the challenge. These products are somewhat ‘ahead of their time’ and customers are still unfamiliar with them.
Shawna Ducharme, principal engineer for product innovation at the CIC said more work needs to be done on methods for assessing crop quality.
“In a lot of biomaterials applications there are not readily available standards and not readily developed methods to assess quality,” she said. “We have to identify the most suitable varieties of the crops for use in biomass applications.”
There’s also still work to be done to identify agronomic best practices for growing and harvesting crops so that their fibre is optimized, and research continues on how to optimize the strength and durability of biocomposites.
The CIC’s Fibre City Initiative is now working in these areas, Ducharme said.
“Essentially it’s a fibre-grading laboratory and the idea is to be a global centre of excellence in assessing fibre quality and developing standards for quality grading of biofibres,” she said.