“That’s what our great-grandfathers built
everything out of here on the Prairies – poplar.”
– JAKE SIEMENS
Too many trees is a nice problem to have.
The most common solution, it seems, is to hire a bulldozer and push unwanted bush into big piles and burn them.
While it may be expedient, it is wasteful, since even the crooked ones can be bucked up, split and sold for firewood.
The biggest, straightest ones can be sawn into rough lumber for keeping the woodpile nice and dry, or sold to the neighbours for windbreak boards, building livestock pens and shelters, a henhouse, or even a big timber-frame barn for truly ambitious types.
Read Also
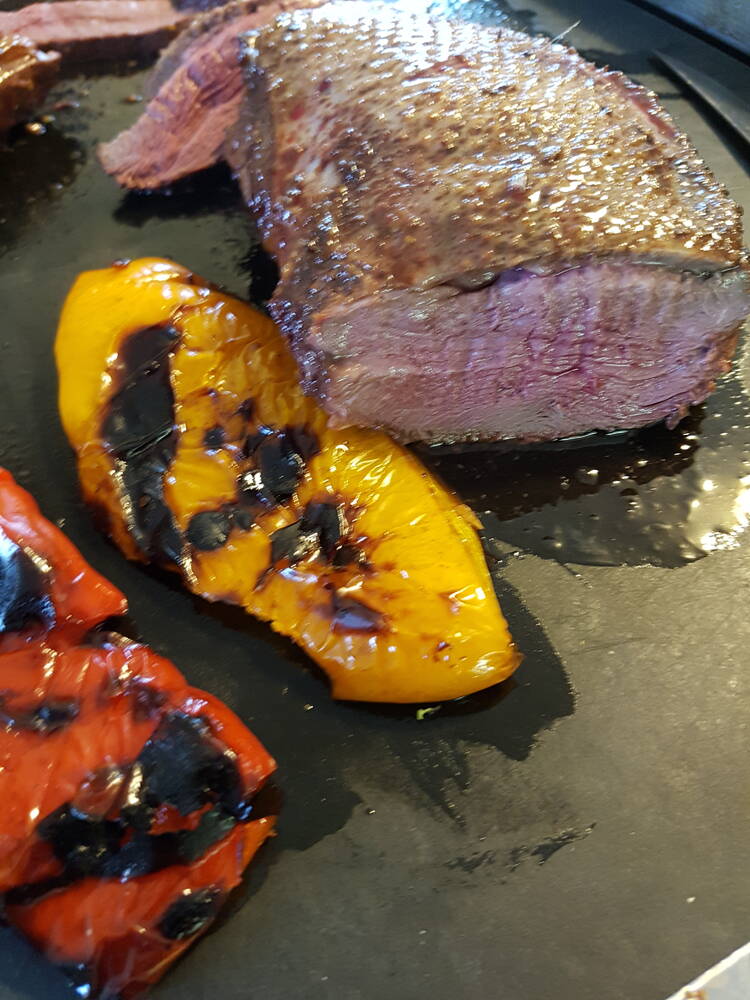
Giant Canada geese have gone wild in Manitoba
Giant Canada geese are seemingly everywhere and can be fine table fare for local hunters, but 70 years ago, they were borderline extinct.
But to do that, you need a sawmill.
A quick Internet search will turn up dozens of bandsaw mill manufacturers all over North America with dealerships in Ontario and Alberta offering machines of any size to fit any budget.
If you want to buy local, the only outfit in Manitoba is Little “Dust” Sawmills in Selkirk.
Owned and operated by Jake Siemens and his family for almost 30 years now, Little “Dust” has been welding square tubing into saw frames and tracks for buyers all over the continent. Lately he has contracted out the actual manufacturing, and generally has two sawmills in the shop at various stages of being built at any given time, depending on orders.
DOLLAR BLUES
“The last couple of years have been a bit tough, because when the American dollar goes down, we don’t sell anything to the States,” he said. “And the price of steel has been choking us pretty bad.”
Unlike circular sawmills, or the low-budget chainsaw-mounted option, bandsaw mills zip through the logs with only a one-eighth inch kerf with very little waste – hence the name Little “Dust,” said Siemens, who also has a hand in a number of family businesses, including trucking, made-to-order small log cabins and a truck-mounted crane that fits into a regular pickup receiver hitch.
With the other types of mills, especially chainsaw units, squaring up a log into a cant on four sides means each of those three-eighths inch or larger passes can add up, turning what would have been a 6×6 into a 5×5 or smaller.
If boards are the desired product, then even more of the log gets turned into sawdust with every slice.
And when cutting hardwoods like ash or oak, the chainsaw mills go from sharp to dull pretty fast. In high-value woods, of course, the waste is all the more painful.
Siemens used to make a half-size mill for the hobby market, but found that he couldn’t square his cost of production with buyer sticker shock.
ONE SIZE
Now he has settled on just one size, capable of sawing a 30-inch-diameter log up to 21 feet in length, for $16,900, complete with road-ready tail lights on a trailer frame.
Unlike circular sawmills, which require a massive engine to power the spinning blade, a bandsaw is easier, cheaper and much safer to operate. With less torque involved, there is no danger of kickback from the blade binding up in the log – a problem that led to countless injuries in the olden days of sawmilling.
“You can teach somebody how to use it in a matter of minutes,” said Siemens. “It’s a one-man operation, but with two people it works really swift.”
He said that about one-third of his customers are farmers and ranchers, while remote northern First Nations reserves account for another third, with the rest bought by retirees who wish to keep busy with a cash-generating sideline that doesn’t require a regular time commitment.
“They are just amazed. Lots of them call me up and say, ‘We should have done this years ago,’” said Siemens.
“One guy wouldn’t tell me how much money he was making, but he said it was way more than both his pensions put together. He said, ‘If I want to work, I
work. If I don’t feel like working, I don’t.’”
Many people assume that only spruce and pine are worth cutting for lumber, but Siemens said that many people who try poplar find that they prefer it to the more commonly used softwoods. It takes a nail or screw easily when still green, and has the advantages of great strength, no sap and less tendency to splinter.
“That’s what our great-grandfathers built everything out of here on the Prairies – poplar.”
EXCELLENT QUALITY
Chris Reynolds, a MAFRI business development specialist and woodlot forester based in Gladstone, said poplar lumber can be of excellent quality if it is handled properly.
“A lot of people don’t like to use it because they don’t understand how it needs to be dried or how to use it properly,” he said, adding that the main reason finding top-quality poplar saw logs can be difficult is because forests in Manitoba haven’t been managed properly for decades and are in decline.
“A lot of the older poplars that would have been good 20 years ago are rotting. But when you can find them, they make beautiful lumber.”
Also, because like all deciduous tree species it is classified as a hardwood, it doesn’t need a costly lumber grader’s stamp, which is a common building code requirement for wood used in construction projects.
“Hardwood lumber has no grade requirement, and poplar is included,” he said. “It’s only spruce, pine and fir that have to be graded.”