As warm weather engulfs the province many Manitobans are dreaming of summer days at the cottage.
And, says one owner of a Manitoba ready-to-move (RTM) company, increasingly those thoughts are centred on cottages that are RTM products.
“Over the past 10 years, cottages have become more popular,” says James Zacharias, owner of Emjay Homes in Austin, Man. “Our business has noticed that about 25 per cent of our builds in a year are destined for cottage lots.”
When customers explore their options around building a cottage from scratch, they often will find that the costs to build a new cottage can quickly add up. This is because most customers have to hire a construction company, purchase the materials, and have them delivered to often-remote locations. Once those steps are done, many still have to hire contractors for final tweaks before the cottage is livable. The costs of transportation, labour and contractors can often increase budget or project delays substantially. As a result, many people are turning to the convenience of pre-built RTMs for their dream cottage.
Read Also
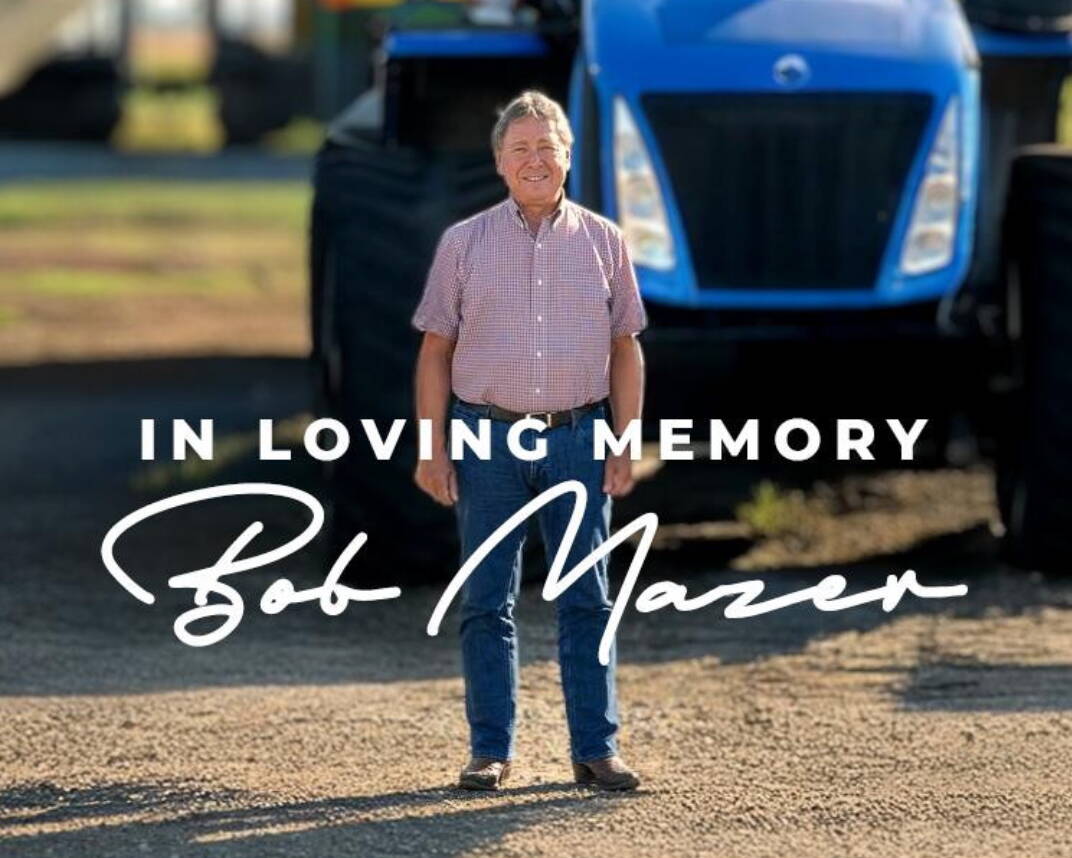
Mazergroup’s Bob Mazer dies
Mazergroup’s Bob Mazer, who helped grow his family’s company into a string of farm equipment dealerships and the main dealer for New Holland machinery in Saskatchewan and Manitoba, died July 6 from cancer.
“We pretty much do everything here in-house that you would pay a construction company or contractors to do,” says Zacharias. “From the first day that a customer decides to build an RTM for their cottage, we are with them every step of the way. We will design their blueprints, order the materials, build the RTM on site, install the exterior and interior finishes and arrange the delivery.”
- Read more: RTM building process lowers waste
As with any RTM product, the customer will need to have a pre-existing foundation on their lot that adheres to local building code regulations. Zacharias says hiring a local contractor to build the foundation will help lower the travel costs often associated with non-local construction companies.
Cottage RTMs are much like residential RTMs in that the customer has a lot of freedom with design. For example, the RTM company can build to the customer’s exact preferences, such as adding customized siding that gives the cottage a log cabin look. Still, Zacharias has found that most of his cottage RTM owners have kept their buildings to more traditional shapes and sizes.
“I have found that most cottage RTMs tend to stay consistent at one level in height and in standard sizes,” he says. “This is because once you build an RTM that is two storeys or is an irregular shape, you may need to lift or remove Hydro lines along the route during the move. Also, with a larger truck, moving costs would be higher and need to be considered in the planning stages.”
Zacharias says that the time period from when the customer decides they want to purchase an RTM to the time that it arrives on their lot is about three months. Zacharias says he offers the same heartfelt tip to all potential cottage RTM owners.
“Do not cut corners when designing your cottage RTM, he said. “Cottage RTMs are very similar to the home build RTMs. I see a lot of customers who come in looking for a cottage and think that they are able to cut corners. In the short term, this may save you a few extra bucks. But in the long term, you will find that there will be some problems, which will cost you. Treat your cottage RTM as if it was a regular home build. These cottages face similar, in fact, usually worse elements than the regular RTM. Keep that in mind when you are planning your building.”
Timeline for RTM builds
RTM builders pride themselves on their customer-friendly approach. According to James Zacharias of Emjay Homes, a project will usually take three months from start to delivery:
- Day 1: Customer has decided that they are going to build an RTM. They will come into the office and meet with the designers to go over their specifications to begin designing the blueprints.
- Day 14: The blueprints will be designed and sent to the customer for approval. Once approval is received, materials will be ordered.
- Day 21: Materials will be delivered to the building shop. Once materials arrive, construction will begin.
- Day 49: Construction of the frame will be completed. The building will be built to “lock up” which is an industry term which means that you will be able to lock the doors of the building and no one will be able to get in.
- Day 56: Interior construction such as electrical wiring, drywall and plumbing will begin.
- Day 60: Siding will be installed and exterior painting will begin.
- Day 70: Interior painting will begin.
- Day 77: Finishing touches will begin such as flooring, trim and installation of interior doors.
- Day 85-90: Building construction will be completed and delivery will be scheduled.
- Day 90: Delivery of the building to the customer’s lot.
These times are based on the average RTM build. Various elements may cause the timeline to vary.