“We looked at the total picture of the diversified farm, and I think it was a pretty good system, but you just can’t survive these kinds of prices.”
– ROBERT MCLEAN
Even the operations designed to finish hogs without huge capital costs haven’t been spared from the slump in industry profitability.
Biotech housing operations made a splash a few years ago, offering farmers a way to get into the hog-finishing business without sinking a pile of money into the concrete, slats, manure lagoons and climate control systems found in modern, large-scale pig barns.
Read Also
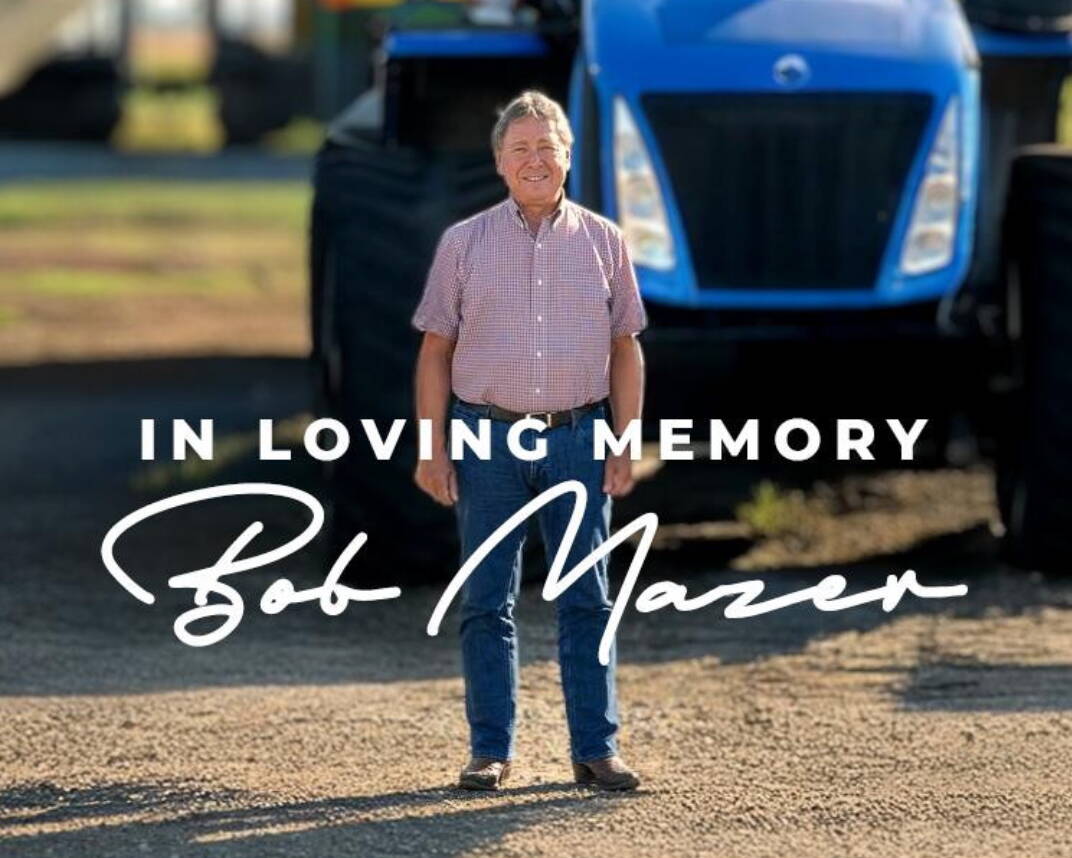
Mazergroup’s Bob Mazer dies
Mazergroup’s Bob Mazer, who helped grow his family’s company into a string of farm equipment dealerships and the main dealer for New Holland machinery in Saskatchewan and Manitoba, died July 6 from cancer.
Resembling a small wooden corral with bent steel hoops overhead holding up a giant tarp to keep the weather out, a biotech hog shelter could be thrown up for anywhere from $10,000 to $20,000 in a fraction of the time needed to build conventional housing.
Manure management was touted as simpler, too, since the hogs are kept knee deep in straw, and odour was kept to a minimum. A farmer could scoop all the manure out quickly with a Bobcat loader, pile it up for composting, and spread it on his fields as nutrient-rich fertilizer.
“That was my total farm plan,” said Robert McLean, who raised hogs in biotechs on his farm near Manitou for 15 years. He expanded the pigs-on-straw and cattle operation about five years ago after his son Don came back from university.
NUTRIENT MANAGEMENT
At the time, he figured adding hay to his rotations would pull up the nutrients that had gone into the subsoil after years of cropping grains, and a portion of the grain crops would be cycled through the hogs and cattle and spread back on the fields as manure to further reduce fertilizer costs.
“We looked at the total picture of the diversified farm, and I think it was a pretty good system, but you just can’t survive these kinds of prices,” he said.
They finished about 1,800 hogs a year up until last November. The four years previous, they hadn’t turned a profit due to high feed costs and low prices. Now with futures prices at $115 per hog, it doesn’t look like they’ll be stocking the biotechs with weanlings anytime soon.
“When he came back, I said that we really couldn’t afford to expand in land, because grain land was so expensive, so we diversified into cattle and hogs,” he said.
“But of course, looking back now, that was probably the worst mistake you could have made, because we hit BSE, then poor prices in the hog industry.”
PROGRAMS NO HELP
Now, the grain side keeps the farm going. CAIS and AgriStability payments didn’t help at all, because one side of the farm’s revenue balanced out the other.
“There’s way more labour and management with the biotechs, and your feed costs are quite a bit higher in the wintertime, but personally I think we would have done all right with them,” he said.
The McLeans still have their cattle, but he joked that it would take a moment of weakness, a big bottle of whiskey, and $200 per hog to get them back into the hog-finishing game.
David Rourke, who runs 13,000 finishers a year through a hoop-house finishing operation using spent grains from his on-farm, small-scale ethanol operation said that he has lost money on hogs for two of the past six years. The Minto-area farmer also farms 5,000 acres and oversees an agronomic research business.
“We had done fairly well by forward pricing and buying feed at the right price until recently,” he said.
We thought the summer might be a good time to be on cash basis – or at least our advisers did – so we didn’t lock any in. Now we’re suffering along with everybody else,” he said.
“We lost a little bit two years ago, and we made a little bit of money last year, and we’ll probably lose a little bit this year, but I’m not going broke,” he said.
ADVANTAGE
The biotech housing model offers one main advantage over conventional hog farming – it’s easier to pay for, he said. In an operating environment with very thin margins, huge capital costs to pay for over time can be ruinous.
But feed, labour and buying weanlings account for most of the cost of finishing a hog, and low prices can still result in a tidal wave of red ink, even for low-overhead operations.
His highly diversified operations are run as independent ventures, so he is able to tap AgriStability payments separately. That means profits on
the grain side don’t go to subsidize the pigs in a down cycle.
In past years, the manure from his straw-based operation was enough to fertilize a quarter section of grain, but now he finds that it makes more sense to spread it thinner over more acres to supply the crops’ phosphorus, potassium and sulphur needs.
”Heavy applications weren’t giving us the boost that we thought it would, so we’re going with more moderate amounts and supplementing the nitrogen,” he said, adding that research data shows that over time, the increase in organic matter and microbial activity from the compost applications pays off in better moisture retention and soil health.
Straw-based hog farming in the biotech shelters doesn’t mean that the animals are completely disease free, he added. At first, he was able to avoid problems by using different genetic stock, but now he has been forced to medicate to counter low-level but persistent common swine diseases.
MARKETING
Rourke said that in the past, he had kicked around the idea of direct marketing pork from his Hog Hill Farms venture. But the cost of adding a processing facility at a cost of $7 million plus 25 more employees to his operation was deemed too risky.
Because the profit from slaughter and processing is about equal to the difference between the open market and returns at the retail level, most small killing plants buy only cull hogs.
“Putting my first-grade pigs in there wouldn’t have made any money,” he said. “Maybe right now I might think about it, but at the time it was break-even at best with a whole lot more hassle.”
In theory, the low-overhead biotech model allows producers to go in and out of the hog business quickly. But obligations to employees, contracts, and weanling suppliers mean that he must soldier on through the rough patches.
The hog business is notorious for gut-wrenching highs and lows, said Rourke, and widespread pessimism is usually a good indicator that the market is turning. But three years in a row of bad prices would pull away the AgriStability safety net.
“But if you ask me in another year and it still looks like this, I may well not have any pigs,” he said. “But for now it looks bad enough that I’m optimistic enough that it will eventually turn around.”
Shirley and Herb Watson have 20 biotech barns on their farm near Treherne. They built their first biotech shelter in 1994, then expanded in 2005, churning out about 12,000 hogs a year at their peak.
The biotechs have been empty since February of last year, and are now for sale.
The composted manure was great for their irrigated potato crops, but the losses from finishing hogs just couldn’t be sustained, she said.
“The fertilizer was great. That was working for the potatoes, but the hogs weren’t, so we thought we’d shut it down.” [email protected]