“It’s just a matter of putting the four bunks down, putting the rails in, and then just levelling it.”
– DARYL NEUSTATER
There’s a trick to every trade, so they say.
For low-impact logging, that’s especially true. Put a chainsaw into the hands of the average Canadian, and depending upon how much he or she knows about using it, you might want to stick around and watch what happens next – or hastily flee.
Read Also
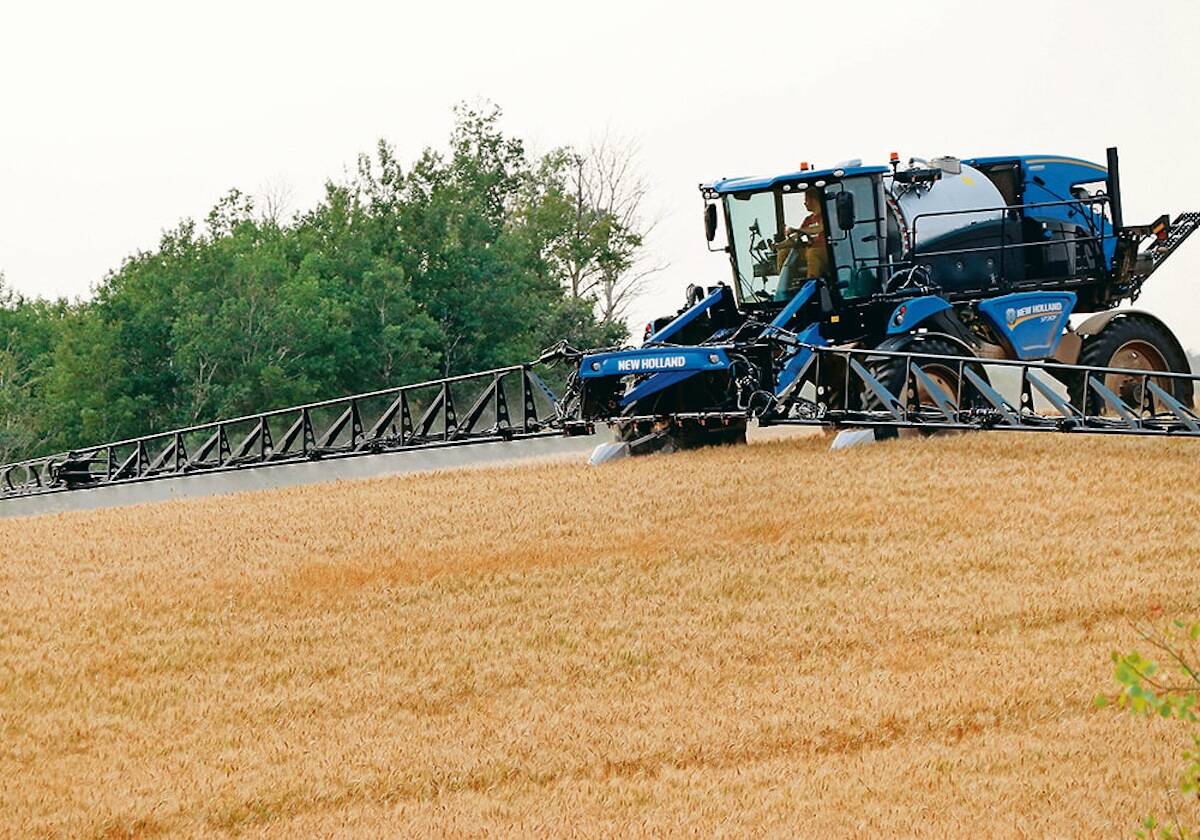
Farming still has digital walls to scale
Canadian farms still face the same obstacles to adopting digital agriculture technology, despite the years industry and policy makers have had to break them down.
At a Low Impact Logging Field Tour organized by MAFRI forester Chris Reynolds and Mountainside Community Woodlands near Onanole last week, a handful of interested participants braved an icy wind to learn about small-scale forestry.
The group also learned a few tree-felling tricks from Daryl Neustater, a professional arborist from Erickson.
TREE-FELLING TRICKS
They saw how some handy tools can make logging a relatively easy job that not only leaves a minimal footprint on the forest, but also serves to improve the health of all the trees over time.
According to Reynolds, being able to drop a jumbo poplar tree in the direction you want is useful for a number of reasons.
You can avoid damage to smaller trees, keep the messy top branches out of the way, and line up the log for easy skidding out of the bush – not to mention avoid a premature end to your logging career.
Neustater’s felling demo left nothing to chance.
First, he pitched a lead-shot filled pouch attached to a length of strong twine through the upper branches of a large poplar. Then, he tied the loose end to a heavy – yet very soft – logging rope. By pulling on the twine dangling down from the crown of the tree, he was able to thread the rope into position and tie it to the tree’s trunk.
Then he fixed a short anchor rope around another tree’s trunk a short distance away, then used a pulley to put tension on the tree in the direction he wanted it to fall.
DIFFERENT CUTS
Next, he fired up his chainsaw and made his first cut on the trunk. Instead of cutting out the classic slice-of-watermelon-shaped wedge, he made a 12-inch, vertical slice on the side he wanted the tree to fall, and then used a short three-inch horizontal cut at the bottom to free the chunk of wood.
Then, he used the nose of his saw blade to bore through the trunk and cut all the inside fibres at the same height as the first horizontal cut, but was careful to leave a one-inch-thick “hinge” of wood to carry the falling tree down safely without twisting, and a “trigger” on the opposite side.
Then, once he looked around to check that everyone was safely out of the way, he “pulled the trigger” by slicing through the last bit of wood that was holding the tree up. With a little help from a tree-felling lever, he was able to gently drop the tree exactly where he wanted it to fall.
This technique not only avoids trapping the saw in the kerf if the tree begins to tilt in an unexpected direction, but it also avoids the dreaded “barber chair” phenomenon, which has killed or injured careless or inexperienced loggers since time immemorial, Reynolds noted.
“BARBER CHAIR” INJURIES
Resembling the high-backed chair used by barbers, a barber chair results when the forces of a falling tree split the trunk higher up instead of at the kerf, and part of the butt swings up with tremendous leverage.
Once the tree was safely down and an eight-foot section had been cut, Reynolds jockeyed a homemade logging arch made from welded square tubing into position over the log. He then attached a chain around the butt, and with a built-in hand crank and grab hook, lifted it off the ground.
With its weight transferred to the skis of the logging arch, made from a slippery plastic snowboard material, the monster log could then be moved and manipulated easily – without aggravating a pre-existing chronic back pain condition.
The ATV was then backed into position, the arch was hooked onto its ball hitch, and the mighty poplar log was towed away to the sawmill up the hill.
TILTING, ADJUSTABLE BLADE
When most people think of a sawmill, they think of either a portable bandsaw or the huge, diesel-powered spinning blades.
The Peterson sawmill, however, combines the portability of a bandmill with the precision and speed of a circular sawmill.
With its tilting, adjustable blade, it can cut both vertically and horizontally on the forward stroke and the back. Unlike a bandmill, it cuts straight through hard knots without drifting. With only six teeth, it takes only a few minutes to sharpen.
The sawmill, which cost $18,000, is composed of a 25-hpa powerhead, carriage, and two large aluminum bunks.
Neustater said that he was able to haul it in and assemble it on a patch of flat ground in less than half an hour. The powerhead, the heaviest part, attaches to a set of wheels so it can be moved like a wheelbarrow.
“It’s just a matter of putting the four bunks down, putting the rails in, and then just levelling it,” he said. [email protected]