A lamb is born prematurely on a Manitoba sheep farm. It weighs only a pound.
To survive, the lamb will need round-the-clock care — more care than the farmer has bandwidth to give, so a woman named Nicole takes the tiny critter home. She and her son put a diaper on the lamb and take it with them everywhere, feeding it regularly with a bottle.
They name it Clover. In 12 weeks, Clover lives to become a strong, healthy sheep that can return to the flock.
The first time Clover is sheared, Nicole gets the fleece. She processes it into yarn and makes a warm, black tuque.
It’s “a really beautiful level of connection to that material,” Anna Hunter, co-director of the Pembina Fibreshed told the Manitoba Co-operator.
It’s the kind of connection most Manitobans don’t have with clothing anymore — the experience of raising animals or plants, collecting wool, fibre or hides, working alongside others in their community or family to process them, and finally producing long-lasting, quality garments.
That’s something the Pembina Fibreshed’s One Year One Outfit Challenge tackles head on.
Throughout 2021, the One Year One Outfit Challenge asked people to make clothing out of materials or dyes made or grown within 200 miles of the Pembina River Valley (zippers and thread not included).
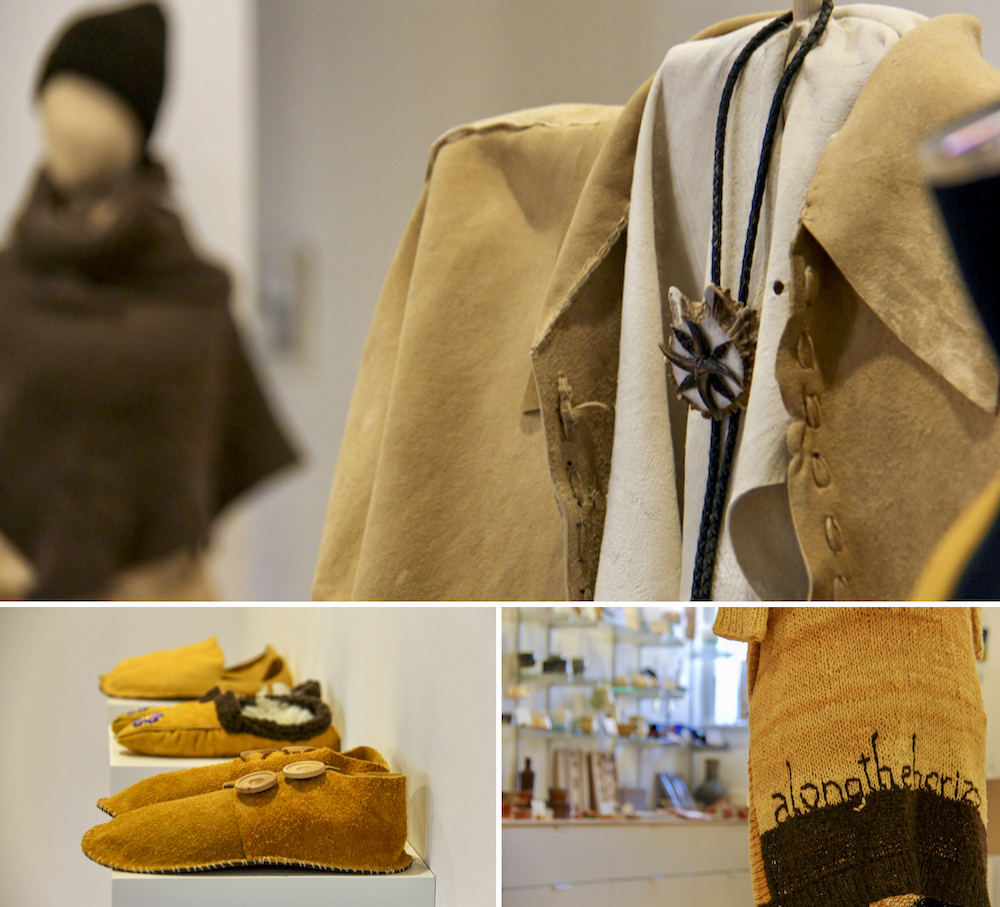
At the end of the challenge, about 20 participating artisans displayed the clothing they made in an exhibit at the C2 Centre for Craft in Winnipeg from February 18 to 26.
Materials used include sheep and alpaca wool that was spun, knitted, crocheted, woven and felted; deer and elk leather; beaver tail; and deer antler.
Connecting with ‘makers’
Karen Enns displayed her grey, red and cream-coloured pullover, tawny-hued sweater and curly locked cowl at the exhibit.
She told the Co-operator that until she went to the Manitoba Fibre Festival about five years ago, she didn’t know anyone else who worked with wool.
“I just found my world,” she said.
Enns, who lives on Rock Creek Farm, a saskatoon U-pick near Grunthal, said she found many new contacts including Anna Hunter — who, besides co-ordinating the fibreshed, raises sheep and processes wool at Longway Homestead near Ste. Genevieve.
The striped pullover is a combination of wools, each with its own story. The cream is ‘rescued’ fleece from a farmer who raises sheep for meat, but just burns the wool. Enns skirted and cleaned the wool and took it to Longway Homestead to have it milled.
The dark wool is alpaca, which Enns got from a farm near St. Malo and processed at Longway Homestead. The red comes from Turtle Mountain Alpacas.
The unique curly texture of the cowl comes from felting wool into a collar, and then punching individual curly strands into it. Enns did this at a workshop in Grunthal.
Mandy Furney displayed a sweater, shawl, hat, bag and mittens at the exhibit. She washed, carded and spun much of the wool herself. She also dyed some of the yarn with plants from her own yard.
“I was just really excited to have the focus to put together an outfit in one year and just to work with other people, and to try some new things,” she said.
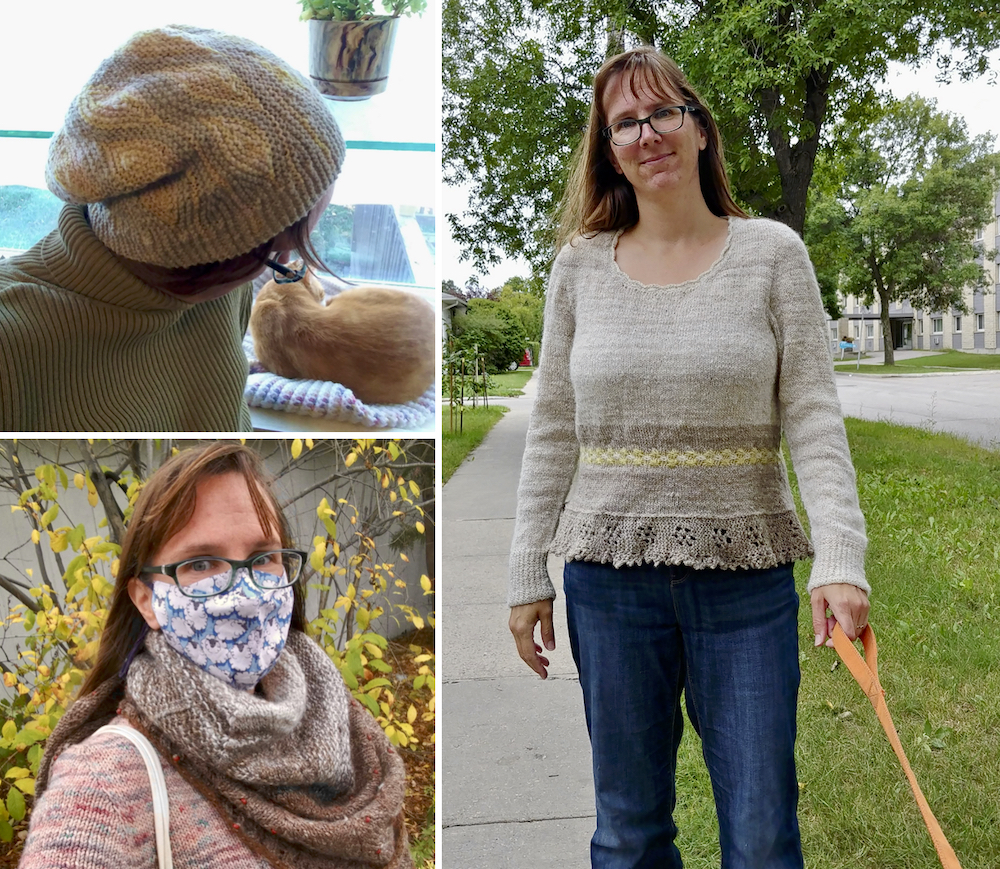
Furney lives in Winnipeg and works in education. She’s well connected with local spinning and knitting groups.
She talked with other group members to find out what they were using to dye textiles, and she found out that the ‘devil’s ninebark’ bush in her yard with its deep-purple leaf would actually produce a neon-yellow dye.
She also rescued fleeces that were destined to be discarded. She washed them in her yard, picked them through for good wool, then spun that on a spindle or spinning wheel.
Those items might sound like something out of a children’s storybook, but there are actually quite a few accomplished spinners in Winnipeg, Furney said.
“A lot of people don’t know,” she said.
For her, the challenge was not just about making items, but about connecting more people with local resources — including spinning and knitting groups that could help them get started.
(Re)connecting with clothing
But why go through all that work, the Co-operator asked Hunter — the washing, spinning, knitting, or tanning and softening of leather? Why take weeks or months to make an outfit when they’re readily available down the road at the mall?
It’s true — clothing is cheaply and readily available, said Hunter. But a $5 price tag on a sale rack T-shirt doesn’t reflect the true cost of the item. “Let alone the labour that goes into growing those textiles… and then the labour of actually sewing it and manufacturing it, and then the shipping costs and the environmental costs.”
In recent years, the environmental toll — the sheer amount of waste — caused by “fast fashion” has come into the spotlight.
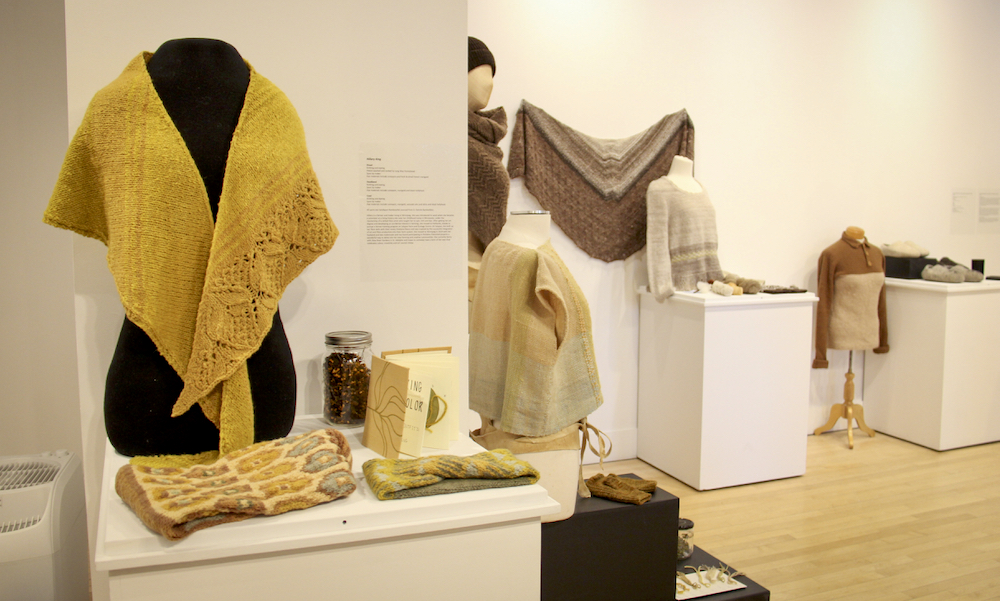
Metro Vancouver residents, for instance, throw out about 20,000 tonnes of textiles each year — the equivalent of 44 T-shirts per person, according to a Feb. 28 CBC article.
Across North America, about 10 million tonnes of clothing go into landfills every year, according to Waste Reduction Week in Canada’s website. About 95 per cent of that could be reused or recycled, it added.
In the U.S., that amount has spiked sixfold since the 1980s, wrote the Centre for EcoTechnology (CET).
CET writes that “fast fashion,” which mass produces clothing at low prices and encourages consumers to buy new styles regularly, has magnified this problem. Companies push new, cheap styles into racks and people buy more than they need — thus being less likely to value the clothing enough to hang on to it when it’s slightly out of style, or needs mending.
As a result, enormous amounts of water, electricity, material and labour go into products that are worn a few times, then binned.
For Furney, the One Year One Outfit Challenge ties into her mindset of reducing fashion waste.
“We do a lot of second hand and lots of mending,” she said. It’s not easy with young kids, she added, but second-hand stores are a big help.
She said she’s found if she makes the items herself, they’ll last a long time and will be easier to mend than commercially produced clothes.
“And just the fun of the process. I like things to custom fit, and they’re unique,” she added.
The spirit of the One Year One Outfit Challenge is to treat clothing with respect and to value and acknowledge where it comes from, said Hunter.
“We need to return to a place of knowledge around these skills, and it’s a lot more fun to do that in community,” she said.