The yields are getting larger, the machinery bigger.
It stands to reason that grain storage bins have had to get bigger as well. Smaller bins and their effective grain-drying systems in place for years are being replaced by larger bins and more intricate drying needs to handle the larger contents.
“There are larger bins in use all across the Prairies,” said Lorne Grieger, a senior official with the Prairie Agricultural Machinery Institute (PAMI) from his Portage la Prairie office. “And because of this, there is a lot of interest from producers as to the different technologies and systems for grain drying in these bins. There is more grain stored in these bins, and therefore there is higher risk if something goes wrong.”
Read Also
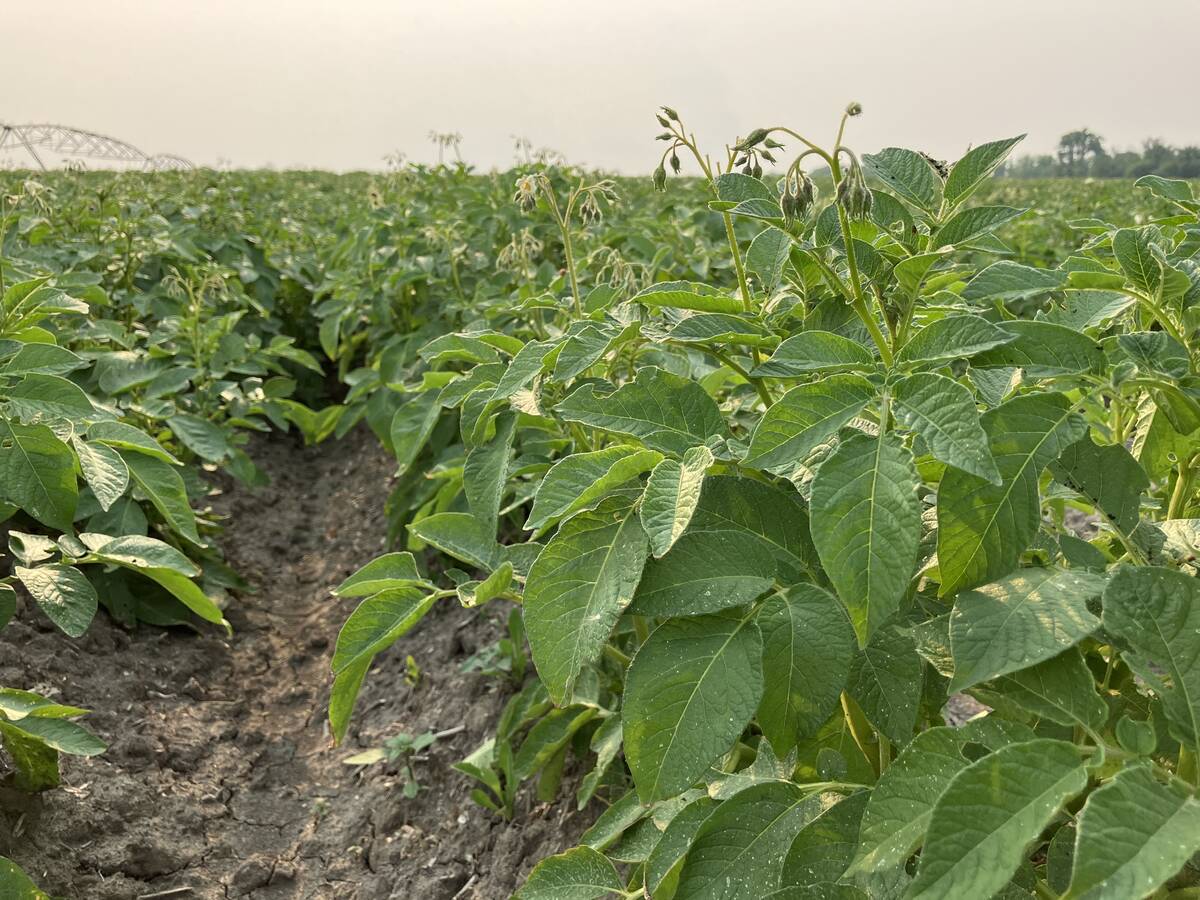
Potatoes join Innovation Farms testing ground
New MacGregor site adds potato farming to FCC and EMILI’s agriculture tech initiatives in Manitoba.
PAMI’s mission is to enhance sustainability and profitability in agriculture and other sectors through research, innovation, adaptation and knowledge transfer. Grieger specializes in grain-drying systems and understanding the complex relationships between grain and airflow.
“All types of grain storage and aeration requite proper monitoring and management,” he said. “Understanding what is going on in the bin leads to better management decisions by the producer.”
The key to that is understanding the difference between aeration and natural air drying and the different requirements of each, he said. A general rule of thumb is natural air drying needs 10 times the airflow rate compared to aeration.
“Aeration is cooling and conditioning the grain. If air is cooler than the grain, the grain will cool,” he said. “Natural air drying is reducing the moisture in the grain.”
Most grain bins are designed to push air through the grain from the bottom of the bin. The air is pushed upward through the stored grain and exits at the top of the stored grain and out the top of the bin.
However, there are other systems as well. Grieger said the various grain-drying systems come with different styles of fans and air distribution. Collectively, they can all provide airflow that depends on resistance to airflow — or static pressure — that depends upon grain type, depth of grain, airflow rate (faster that air is pushed in, the greater the resistance) and the ducting that distributes evenly throughout the bin.
A 2011 study done by the University of Nebraska-Lincoln on management of in-bin natural grain-drying systems to minimize energy cost summarized that “picking the right type of fan, based on the anticipated static pressure required, saved 33 per cent of the horsepower and electrical energy cost compared to making the wrong choice of fan.”
Grieger, who pointed out the excellent work of his colleague Joy Agnew of the Saskatchewan PAMI office on grain-drying systems, said the most critical decision that producers need to make before they purchase grain bins is determine what exactly they need and want the system to do.
“By matching the right system with the producer’s needs and understanding the physical processes involved, a producer can ensure quality, as well as save time and energy,” he said. “But they have to be as certain as possible of the intricacies of what they want to accomplish right from the outset.”