Canada’s poultry hatcheries and supply flocks have just under four months to complete their transition to the Canadian Food Inspection Agency’s new licensing system.
The CFIA sent a reminder of the deadline June 23.
By Nov. 9 of this year, under the new rules, flocks and hatcheries with CFIA permits must have a preventive control plan written and in place. That plan must describe “operational hazards and how to mitigate these risks,” the June release said.
Additionally, flock owners will have to obtain eggs and chicks from farms that also have a written plan, and any incoming eggs will have to come from operations that employ bacteria testing. The agency linked the latter requirement to efforts against food-borne illness.
Read Also
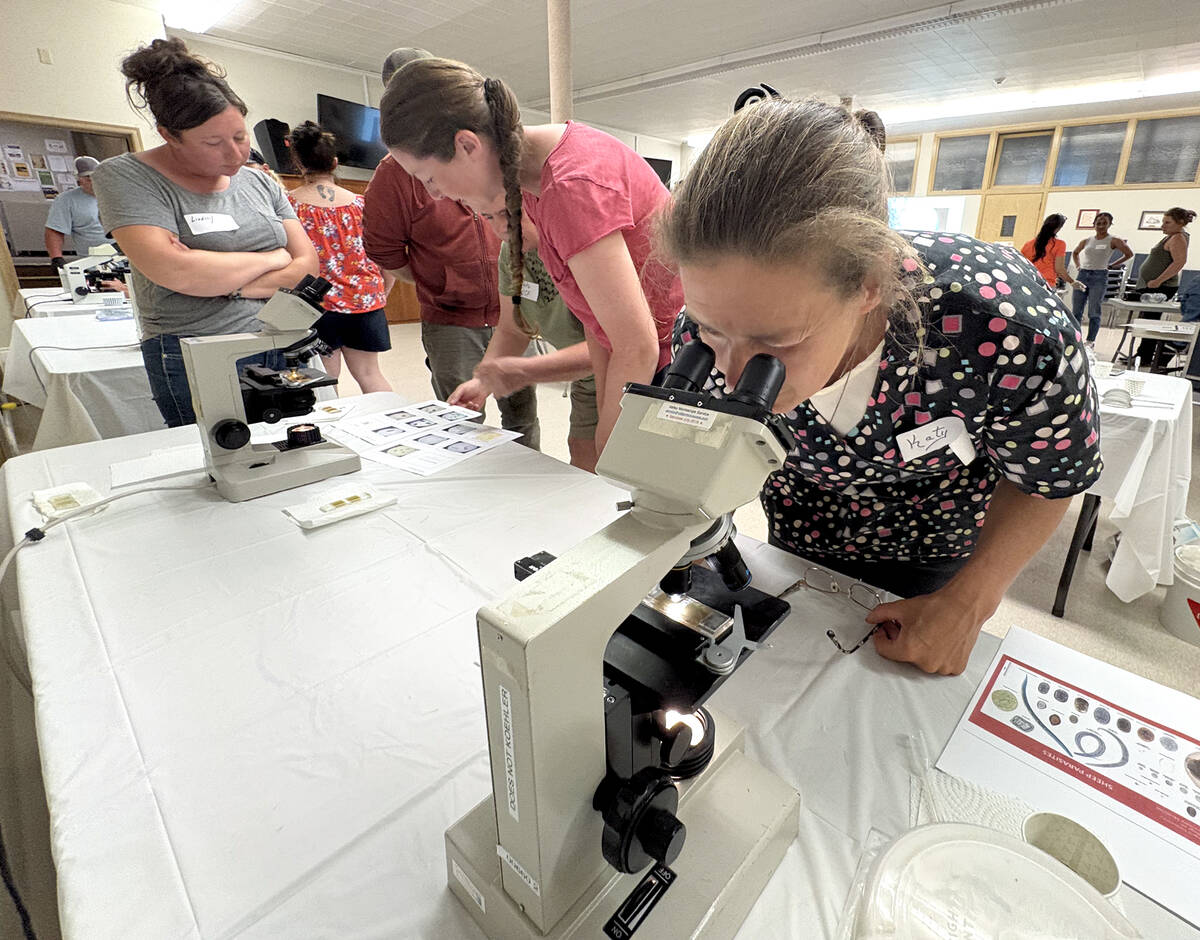
Smart deworming for sheep starts with individual fecal egg counts
Fecal egg count tests are one step to managing dewormer resistance and managing sheep parasites on Canadian sheep farms to maintain flock health.
Egg and chick supplying farms must adhere to the Canadian Hatchery and Supply Flock Testing Standards, the CFIA said.
According to a guidance document from the CFIA, producers may not need to do much different to develop and implement a preventive control plan. The agency noted many of the requirements echo existing programs like the Quality Management Program or Food Safety Enhancement Program.
According to the agency, the eventual plan must consider:
- process and product controls;
- sanitation, biosecurity and biocontainment;
- pest control and chemicals;
- hygiene and employee training;
- equipment design and maintenance;
- physical structure of the farm, including surroundings and upkeep;
- receiving, transportation and storage; and
- traceability, control and complaints.
For each category, the plan must look at risks, what can be done to control hazards and how risk mitigation will be monitored and verified. There must be plans for corrective action when needed, plans for an annual review and information on how all of that will be recorded.
“The operator has the option to modify the elements, but all the possible hazards or risks must be identified,” according to the guidance document.
“The hatchery operator must then indicate how the hazards in these elements are identified and monitored and then describes [sic] how these could be prevented, eliminated or reduced to acceptable levels.”
Changes were first published in November 2022, with a one-year transition period for the sector to make the switch.