When considering group sow-housing systems, electronic sow feeding (ESF) is likely the best choice for pig producers with high productivity expectations, according to Thomas Parsons at the University of Pennsylvania.
“We now have farms pushing above 30 pigs weaned per sow per year and thus the technology itself, if properly managed, is not a barrier to outstanding production,” he says.
Read Also
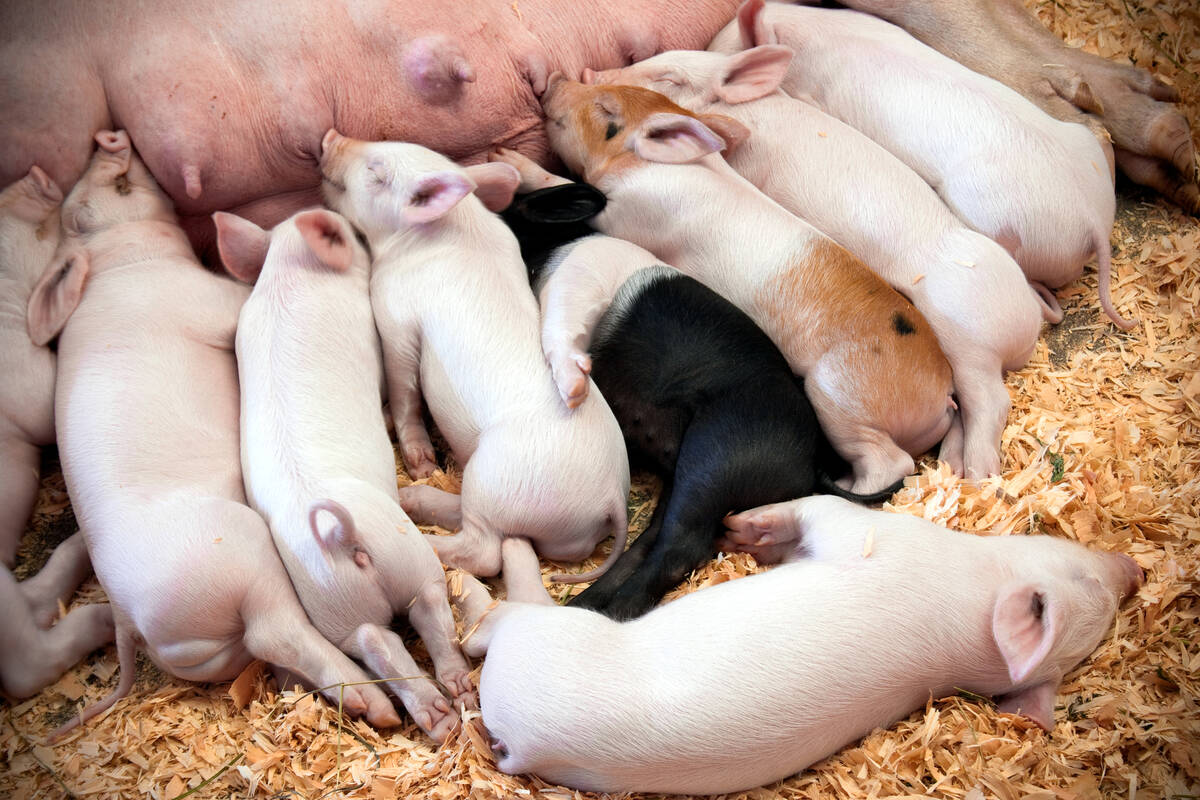
First-time pig mothers may need more lysine
Lysine feed recommendations may fall short for gilt pregnancies when it comes to making sure the mother pig can produce as much milk for her piglets as possible
ESF is the only alternative to gestation stalls that provides true individual animal nutrition, he notes. It also provides the opportunity to further automate sow management — for example spray marking of animals requiring vaccination or selection of animals needing to move to farrowing. Parsons has gained widespread experience with the system in 40 farms with 70,000 sows and has identified the most important design and management considerations.
One key design aspect is to segregate gilts and young sows from the older sows. “When mixed with higher-parity sows, the smaller, still-growing gilt can be at a disadvantage and suffer negative consequences from being at the bottom of the social order,” Parsons explains. “These animals can be fed a different ration than the sows and managed differently, perhaps by being attended to by the best available labour.” The overall objective is to reduce stress and competition in the pen environment, he says.
Dynamic or static groups?
Another fundamental design decision is whether to base the system on a dynamic group of sows or static groups.
“Dynamic flows are required on small farms where the weekly breeding group is less than that supported by a single ESF station,” Parsons points out. “This will range between 50 and 75 sows depending upon the feeder manufacturer.”
Dynamic flow also works well where sows are mixed immediately after breeding, because the 21 day returns can be rebred and just left in the pen, he says. However, the downside to dynamic grouping is that the integrity of the weekly breeding groups is lost as there are sows at all stages of gestation in the same pen, which makes daily management and identification of individual animals more difficult.
Static groups are constituted once, social hierarchy stabilizes, and the group is then left intact for the duration of gestation. There are clear management advantages of working with weekly breeding groups. However, Parsons says variations in weekly breeding targets and any unanticipated fallout from a group can lead to sub-optimal space utilization of the facility. He suggests that the minimum herd size for implementing static groups is 1,400, but most often recommends this method for herds of 2,800 or more.
“Here we would have about 90 sows and 30 gilts comprising the weekly breeding group,” Parsons explains. “We make one static group of about 75 sows per week and then run the gilts and remaining sows in separate dynamic flows. This captures the convenience of a static system, but helps maximize space and feeder utilization as expected from a dynamic flow.”
The time of group formation, relative to breeding, is another important consideration, according to Parsons. Sows may be mixed together within three to five days of breeding or at about 35 days into gestation when they have been confirmed pregnant. The argument for mixing at 35 days is that management in early gestation remains the same as a sow stall system and is easier than when sows are in groups. However, despite this apparent advantage, Parsons says that mixing soon after breeding also works well. “Our experience is that both pre- and post-implantation systems can support good production,” he notes. “Some of our best ESF herds are pushing 28 to 30 pigs weaned per sow per year and are using a pre-implantation system.”
Training pigs and people
Training gilts to use ESF feeders is essential, stresses Parsons. “The key aspects are to get gilts used to stalls prior to ESF training, the use of training feeders modified to accommodate the size of gilts and dedicated training pens with additional gating to facilitate animal control during the training process,” he says. “No gilt should enter the herd without being fully trained as they will become a problem in the future and are at greatest risk of prematurely leaving the herd.”
Sow housing involving large groups of sows is so different to manage compared to sow stalls that the operators need training too. Staff can be resistant to change, Parsons points out.
“It is important that the barn staff is enthusiastic and committed to the project. The barn staff must take ownership of the ESF and the individual animals that it is feeding,” he says. “Less pig experience and an on-the-job worker training program can in some cases be preferable to trying to re-educate experienced workers.”
One of the biggest challenges of moving to group housing is being able to maintain the same level of individual care as can be achieved in sow stalls, Parsons believes.
“In large groups it is more difficult to use the physical location of the animal as the identifier of an animal and or the problem to be managed,” he says. “Thus, barn staff needs to more skilled at identifying individual animals with the group as well as recognizing problems within the pen.” He suggests labelling all physically identifiable locations in the barn to aid communication between staff members and clearly marking sows in need of attention so that they can easily be found in the future. He also recommends using the ESF computer to identify those animals that either do not eat all their ration or eat at the end of the feeding cycle as these are the ones most likely to need attention.