Prairie farmers may need to get used to leaving grain in the field at harvest.
“Harvest might be starting earlier, but poor weather during the harvest season is slowing down that last little bit of harvest, and there’s more and more crop being left in the field in October,” said Joy Agnew, program manager at Prairie Agricultural Machinery Institute (PAMI).
“The more the crop is left out in the field in October, the more likely you’re going to need to dry it.”
Farmers may have hoped that the delayed harvest of 2016 — when cold, wet weather resulted in one of the longest harvest seasons on record — was an anomaly. But conditions in 2018 were actually worse, Agnew said at the Farm Forum Event last month.
Read Also
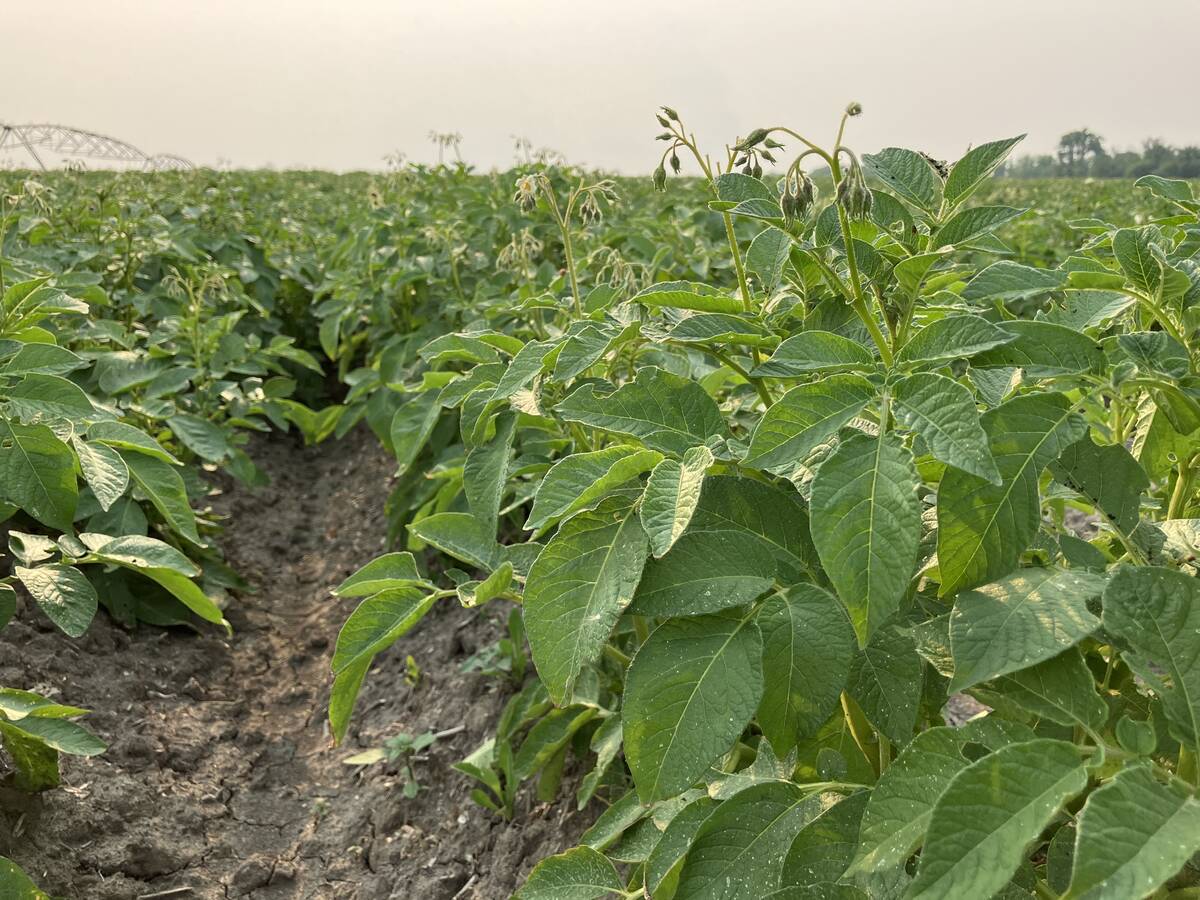
Potatoes join Innovation Farms testing ground
New MacGregor site adds potato farming to FCC and EMILI’s agriculture tech initiatives in Manitoba.
Despite an early start, a wet September created delays and by month’s end, average temperatures in Western Canada dropped below 10 C — the sweet spot for in-field natural air drying. In early October, the majority of crops in the province, save in the south, were unharvested.
“In 2016, there were 370 million bushels left in the field by early October, but this year, there were 439 million bushels,” said Agnew.
She called 2018 “a bad year” — but more worryingly, said this trend toward a later harvest is likely to continue, as weather patterns change, farms get larger, and longer-season varieties become the norm.
Between 2007 and 2012, two of six harvests were less than 80 per cent complete by Oct. 9. But that has more than doubled over the past six years, with four (nearly five) out of six harvests less than 80 per cent complete by Oct. 9.
“It looks like harvest may be trending to be later and later,” said Agnew.
Reducing spoilage risk
And if that’s the case, proper grain storage will become even more important, she added.
“Crop that comes off the field either wet or hot, or both, has potential for spoilage during storage in the bin,” she said. “It’s not enough to have it cool or dry. It has to be both cool and dry to minimize risk of spoilage.”
Normally, producers can control the temperature and moisture in the bin by blowing air through it. But a common misconception is that blowing air through the grain will both cool and dry it, when they’re actually “two fundamentally different things.”
Blowing air through the grain to cool it — known as aeration — can be done with relatively low airflow rates, around 0.1 to 0.2 cubic feet per metre (cfm) per bushel. But blowing air through grain with the intention of removing moisture requires much higher airflow rates, of at least one cfm per bushel.
PAMI compared three different airflow rates (0.1 cfm, one cfm, and two cfm per bushel) for drying peas over a 32-day period. Even though the 0.1-cfm-per-bushel rate did dry the peas somewhat, it only brought their moisture content down from 19 per cent to 17 per cent — and peas are considered safe to store at 16 per cent moisture.
“We ran this fan for 32 days and still didn’t even get it to a safe to store moisture content,” said Agnew. “On the other hand, the one cfm got us to safe to store within nine days and the two cfm got us there within four days. The more airflow we had, the faster the drying we had.”
A heated air-drying system, which uses high temperatures and airflow rates, removes moisture quickly, but a better alternative might be natural air drying with supplemental heat. It uses relatively low airflow rates (0.75 to two cfm) while adding either direct or indirect heat upstream or downstream of the fan to increase the temperature by 10°.
“You’re not turning your bin into a heated air-drying system,” said Agnew. “You’re just tweaking Mother Nature a little bit and turning a poor drying day into a good drying day.”
Air drying with supplemental heat
This relatively new approach is underutilized because “a lot of people don’t understand how to manage it effectively,” said Agnew.
“People think that if warm air is good, hot air is better. But it’s not.”
Heated air-drying systems use temperatures of up to 90 C, with an average of around 75 C, but also have high flow rates — basically the equivalent of 20 cfm per bushel. Those higher heats require higher airflow rates because, while it’s the temperature that draws the moisture out of the grain kernel, it’s the airflow rate that pulls the moisture out of the bin.
“If you’re using really high temperatures, you might be pulling a lot of water out of the grain, but it’s not going anywhere. It’s still in your bin. It’s still sitting there, and your grain is steeping in it.”
Lower airflow rates in supplemental heating (around one cfm) limit the temperature that can be used.
“You need to match your water removal rate from the kernel, which is your temperature, to your water removal rate from the bin, which is your airflow rate,” said Agnew. “Based on what we’ve seen from our trials this year, a temperature increase of about 10° matches the water removal rate of one cfm per bushel.”
That makes sense — good drying weather for most grains requires temperatures above 10 C.
“We get out of good drying weather in mid-September — right at peak harvest season,” said Agnew.
“Because our average daily temperatures at that time drop below 10°, that’s where supplemental heating can really play a role. If we just bump that temperature up by 10°, we extend the drying season.
“You’re just adding 10 C of air and turning a bad day into a good day.”
Cost comparison
Though there is minimal capital investment for either heating system, fuel costs can be high.
Natural gas is currently cheaper than propane and has slightly lower carbon emissions, which is important for producers in provinces with a carbon levy.
“For a 5,000-cfm system where you’re increasing the temperature by 10°, your fuel cost is going to run between $0.70 per hour and $2.50 per hour, depending on the fuel type.
“The electricity to run a 10-horsepower fan is going to be about 75 cents an hour, so if you have natural gas, your fuel is actually cheaper than your electricity.”
The costs for heated air drying range from 20 to 30 cents per bushel, while natural air drying with supplemental heat is around six to 10 cents per bushel.
However, natural air-drying systems take longer to dry grain, so producers will need to make sure it pencils out based on the length of time it will need to run. Heated air drying 5,000 bushels of grain with propane, for instance, costs about $25 an hour, and it could take between half a day and a full day, for a total propane cost of between $375 and $600.
For the same amount of grain in a natural air-drying system, the propane might cost about $2 an hour (because the air isn’t being heated as much), but it might take anywhere between five to 21 days to dry.
“If it takes five days, you’re in pretty good shape. Your propane costs are only $240,” said Agnew. “But if it takes 21 days or more, your propane cost is quite a bit higher than a heated air-drying system.
“Natural air drying with supplemental heating has to be relatively efficient for it to be cheaper fuel-wise than heated air drying. The fuel costs can be really high if they are mismanaged.”
But despite the costs, both natural and heated air drying are likely to become a higher necessity as weather patterns shift and harvests trend later and later, said Agnew.
“As soon as harvest has to happen in October, in-bin drying and heated air drying are going to become more and more common.”
This article was originally published on the Alberta Farmer Express.