Bernie Peet is president of Pork Chain Consulting Ltd. of Lacombe, Alberta, and editor of Western Hog Journal. His columns will run every second week in the Manitoba Co-operator.
The trend to heavier hog carcass weights benefits both the producer and the processor, said two speakers at the recent Banff Pork Seminar.
Ron Gietz, with Alberta Agriculture and Rural Development, pointed out that selling more kilos of pork per sow led to higher producer margins. Jason Manness, procurement director with Maple Leaf Foods, said that packers are demanding heavier carcasses in order to reduce unit costs in the plant by processing more kilos of pork in the same facility.
Read Also
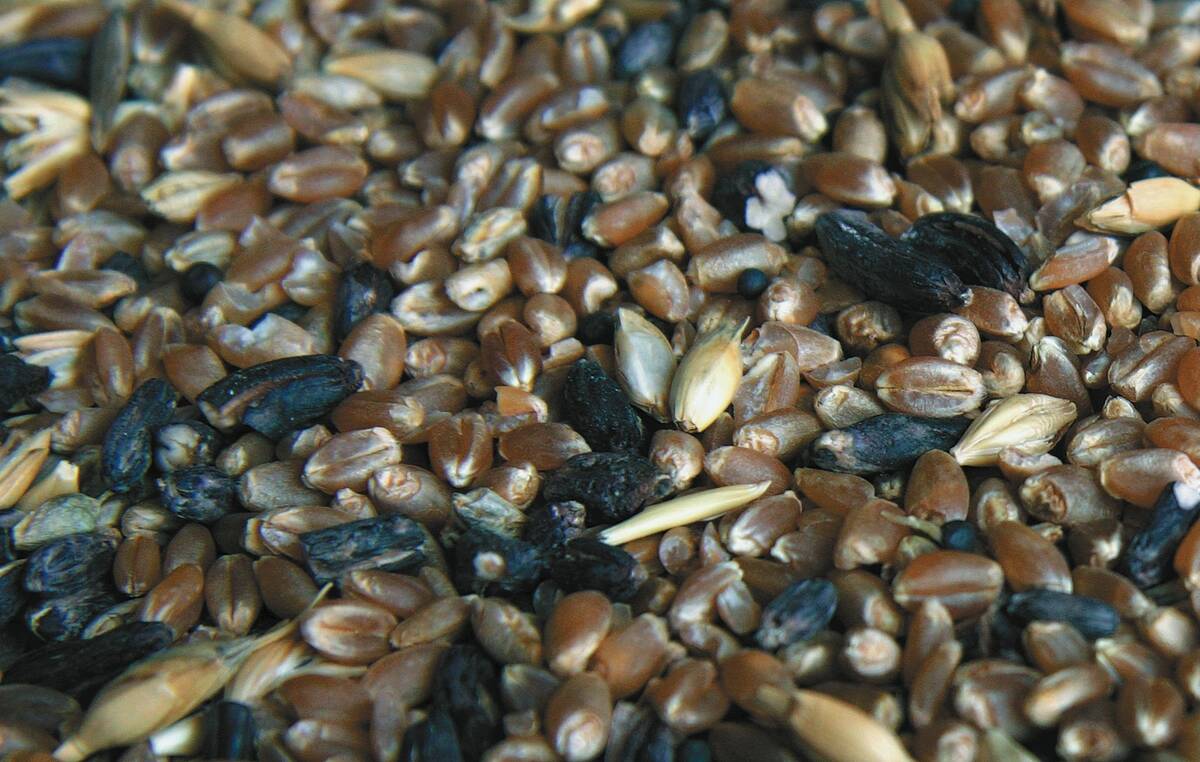
Feeding ergot: research on ergot-impacted grain and beef cattle continues
Saskatchewan research hopes to tease out better ways for Canadian beef farmers to manage ergot consumption in their herd’s feed
Gietz demonstrated how modelling a typical production system could show the effect of various strategies for increasing carcass weight.
“The George Morris Centre adapted its hog cost-of-production model to demonstrate the impact of increasing carcass weights from 92 to 95 kilograms, and from 95 to 98 kilograms,” Gietz said. “This was based on a typical 500-sow operation with 3,850 finishing places, a market hog price of $1.50/kg and a feeder pig price of $2.10/kg.”
Gietz said one of the key factors addressed by this model is the capital cost and physical barn constraints resulting from increasing carcass weights. The baseline operations at 92 kilograms and 95 kilograms are assumed to be finishing hogs near capacity.
“When carcass sizes increase to 95 and 98 kilograms respectively, as proposed, space issues are created,” Gietz said. “The model addresses these challenges by assuming actions such as selling off weaners or accessing underutilized capacity. Another solution might be to finish hogs off-site.”
Table 1 shows the results the model predicts for increasing carcass weights from 92 to 95 kilograms and from 95 to 98 kilograms, based both on selling weaners and by changes to capacity utilization in the barn.
The model shows that the cost per pig is slightly lower if a way can be found to finish all the hogs to market weight rather than selling some as weaners. Potential ways of finishing more pigs include increasing weaning weight, which will improve growth rate to market, achieving faster growth rate in the grow/finish stages and better barn space utilization.
Producers should be able to lower per-kilogram costs and break-evens in the move to increase carcass weights by three kilograms, Gietz said.
“The best results come from squeezing more pounds of pork out of the same facilities, but even if you have to sell off some feeder or weaner pigs to make room, the heavier hogs still pay off. Overall, he said, increasing carcass weights will be beneficial for pork producers.
PACKER EFFICIENCIES
Manness said there is a significant increase in economic efficiency for the packer in processing a heavier hog. He feels that the Canadian pork industry has been at a competitive disadvantage for years through processing lighter hogs.
“It requires the same labour to process a hog within a fairly wide weight range,” he says. “The more kilos of pork we can put on a shackle, the more revenue we can earn from our fixed investment in the plant, equipment and overhead costs.”
Manness points out that the average annual increase in carcass weight in the U.S. over the last eight years has been 1.3 lbs., while the annual increase over the same period at Maple Leaf’s Brandon plant has been 2.2 lbs. “Although Canadian market weights are still lower than in the U.S., we have reduced the gap by 0.8 lbs. per year.”
Manness said that 2010 was a record year for hog weights in the U.S., with an average live weight of 270.5 lbs. (122.7 kg) in the Iowa/south Minnesota region.
Manness said initial 2011 weights are six pounds heavier than one year ago. The target carcass weight for hogs at the Brandon plant has increased from 90-92 kg in 2004-05 to 96 kg in 2010, with a current target of 97.5 kg. “These increases in weight have been achieved without any deterioration in carcass quality characteristics such as yield or backfat,” he adds.
PORTION SIZES
Despite the advantages of heavier carcasses to producers and packers, there have been some problems with food-service customers, Manness said. “Portion size increased, which forced them to increase the price to the consumer and this was sometimes a challenge,” Manness said. “We were getting complaints that the larger portion size of ribs would no longer fit on the plates!”
On the retail shelf, the width of loins meant that retailers had to use bigger trays or put fewer chops on a tray. “For the longest time, a consumer could go in and buy four pork chops on one tray for $10 to feed the family,” Manness said. “Now those same four pork chops may cost $12 or sometime there may be only three chops on the tray.”
Overall, the benefits of the additional throughput at the plant outweigh the challenges created by larger carcasses, Manness said. “Maple Leaf’s sales mix is better off with a larger hog,” he said. “We are able to sort out the correct weight specification for our Japanese customers and many Canadian retailers want the bigger loin eye because it’s more attractive to their customers.”
———
BERNIE PEET
Peet on Pigs
———
143.47
Table 1: Costs and break-evens per CKG
Baseline 92-kg carcass Proposed 95-kg carcass
Baseline 95-kg carcass Proposed 98-kg carcass
Cost Per 100 kg CW 144.19
143.53 141.21
Req’d base break-even price 132.28
131.62
131.68 129.55