Researchers and entrepreneurs are delving deeper into the natural properties of crops, as seed stocks for everything from construction resins and boards and panels for buildings and cars to concentrate health foods.
Many of those projects are being funded by the BioProducts AgSci Cluster, brought together as part of BioIndustrial Innovation Canada with funding from Growing Forward 2.
The Sarnia, Ont.-based cluster aims to help new bioproducts get to market through funding, creating networks and supporting bioproducts companies.
At the cluster’s annual meeting in Toronto last week, several companies and researchers with funding from the cluster explained how they derive from and use agriculture products.
Read Also
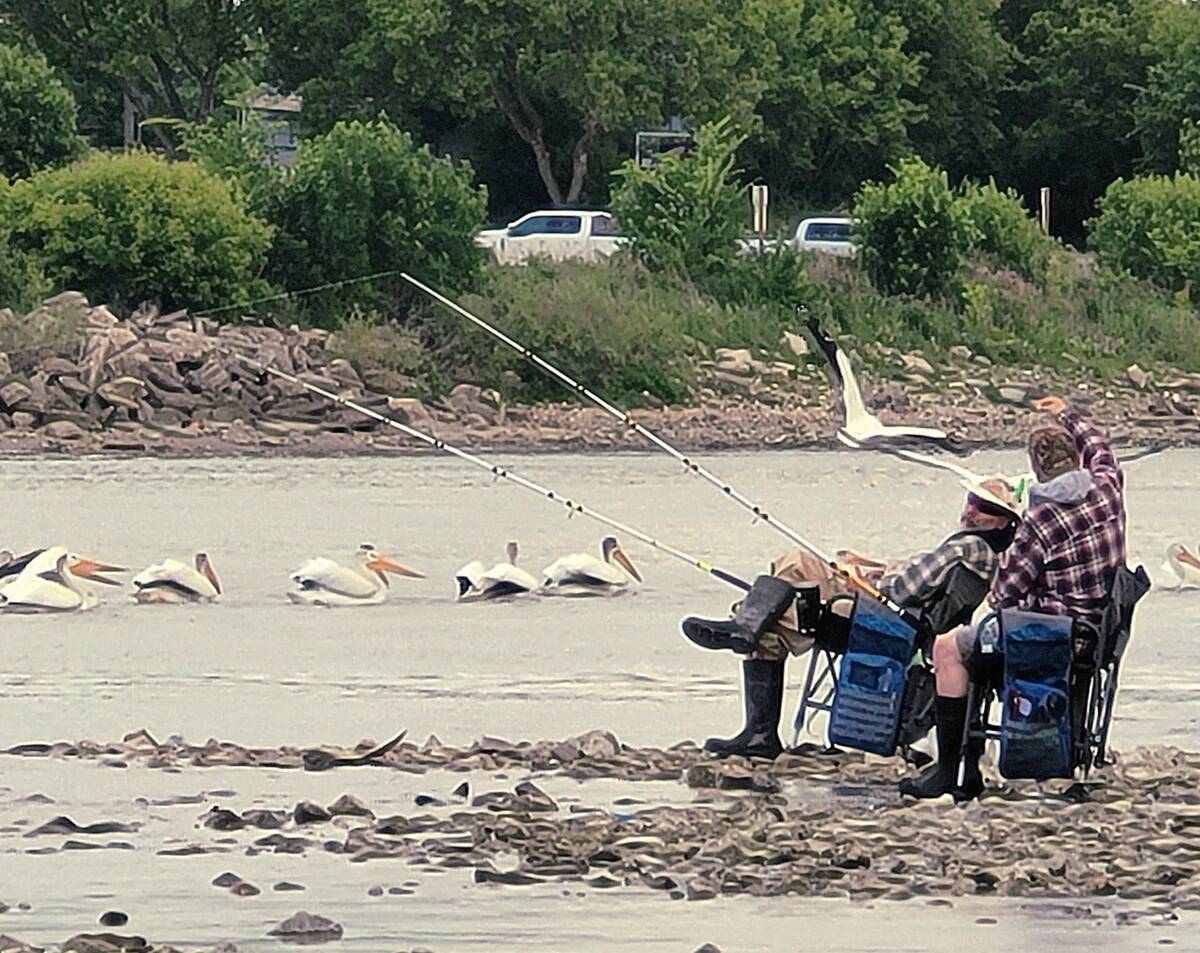
The joys of fishing from shore
Manitoba has many lake and river shorelines to drop a fishing line without the cost of a boat, making shore fishing more accessible, and anglers can still catch impressive fish.
Flax is one of the stars of bioproducts research, both because of the health effects from its seeds and the strength and usefulness of its fibres.
At Prairie Tide Chemicals, president and CEO Dr. Martin Reaney has isolated what he calls orbitides from flaxseed oil.
“Flaxseed is biologically active,” he says. It is high in omega-3 polyunsaturated fatty acids. It also contains lignin, a soluble dietary fibre, and the orbitide component that Reaney has found.
He was first introduced to flaxseed oil research when he was approached to figure out how to eliminate the bitter taste in flaxseed.
“Some people who take it think it tastes awful,” he says.
In doing that research, it set him on the road to isolating the orbitide, a cyclic peptide that dissolves in oil.
“Peptides shouldn’t dissolve in oil, but this one does,” he says.
He believes that the health-positive biological activity of flaxseed oil and flax lignin products are derived from the orbitides.
Beyond health improvement, there are other more complex possibilities from orbitides, says Reaney. They include making light-emitting diodes from flax, which allows them to displace metals from diodes. He also believes he can construct lighter, stronger materials for building materials.
Other researchers are working on a more directly practical use of biomaterials for construction materials.
At the University of Toronto, Professor Dr. Ning Yan is combining wood pulp with flax fibres in order to create biodegradable, lightweight sandwich board panels for use in construction and the automotive sector.
She created a skin for the panels with a higher content of flax, as they wanted the skin to be what holds the board together and gives it rigidity, while the inside, made of wood pulp and a lower percentage of flax, is light and insulating. A mix that includes 10 per cent flax fibre and 40 per cent pulp fibre appears to be optimum, says Yan.
Yan says she can work with any agriculture fibre and hopes to try with others than flax. She says it has been difficult to get a clean, reliable supply of agriculture fibres, like flax.
Ken Mak, a PhD student at Queen’s University reported on the work of the group he is part of, led by Dr. Amir Fam.
They aren’t creating new products, but are using bioproduct fibre products and testing their quality, including resins and epoxys and products that can replace fibreglass. They have found that flax-based materials can replace synthetic materials in applications such as re-enforcing degrading bridges.
At EcoSynthetix, they take low-value agriculture feedstock materials and upgrade them to displace synthetic material.
They make use of polysaccharide from corn and upgrade it through a reactive extrusion process.
The company had its first hit product with a more environmentally friendly coating for paper. The paper business is highly competitive, so they looked, along with some funding, for another industry to disrupt.
They found it in wood composites with no added formaldehyde or isocyanate, says Peter Van Ballegooie, vice-president of corporate development at EcoSynthetix, based in Burlington, Ont.
“We’re all surrounded by wood composites,” he said. “The drivers (of demand for their product) are around health and ecological benefits.”
Their DuraBind product found a market last September with one of the world’s largest producers of composite wood products, the Swiss Krono Group. That group had helped EcoSynthetix develop its DuraBind product, and in the process it found that using their product improved the efficiency of the production pro-cess with less gumming up of equipment.
Sellings of composite wood products, whether they be Walmart or Ikea are all looking for options that off-gas fewer chemicals, says Ballegooie, and EcoSynthetics has options for them.
The major projects funded by the BioProducts AgSci Cluster are at various places in their commercialization, but they are all tied together in their potential to make use of agriculture products, some of which is now left on the field or discarded.